Optimizing Fabric Label Precision with Automated Cutting Systems
The Critical Role of Precision in Fabric Label Production
Why Accuracy Matters in Textile Labeling
Precision in fabric label production is crucial to ensure that all necessary information, including sizing, care instructions, and branding, is displayed accurately. Such thoroughness helps avoid consumer confusion, incorrect garment care, and potential product returns, which can adversely affect both brand reputation and revenue. In fact, statistical evidence highlights that 30% of apparel returns are due to incorrect labeling, underscoring the vital financial role that precise labeling plays in perceptions of quality. By avoiding errors in textile labeling, companies not only maintain their credibility but also foster consumer trust, which is essential for sustaining long-term business success.
Cost Implications of Imperfect Label Cutting
Imperfect label cutting leads to increased waste as manufacturers discard flawed labels, resulting in unnecessary expenses. An analysis of production metrics has shown that even a 1% rise in cutting errors can escalate costs by up to 15% on materials over time. These errors highlight the inefficiency that can arise from inadequate cutting processes, prompting the need for more reliable systems. Investing in automated cutting systems offers long-term savings that can substantially outweigh initial costs by reducing waste and increasing throughput. Therefore, by adopting advanced cutting solutions, businesses can improve efficiency and optimize their resources, ultimately bolstering their profitability within the textile industry.
How Automated Cutting Systems Revolutionize Fabric Label Accuracy
Ultrasonic Technology for Clean Edges
Ultrasonic cutting technology is a standout innovation that uses high-frequency vibrations to ensure the edges of fabric labels are sealed meticulously. This method substantially reduces fraying, a common issue with traditional cutting techniques, by up to 90%. As a result, labels not only maintain a clean and polished appearance but also exhibit enhanced durability. The precision of ultrasonic cutting is crucial in maintaining the label's quality, thereby boosting the overall aesthetics of the branded garment.
Computer-Controlled Pattern Alignment
Incorporating advanced computer software in automated cutting systems allows for unparalleled precision in pattern alignment. These systems are adept at swiftly adapting to variations in fabric, ensuring that patterns are accurately matched. Research indicates that computerized cutting enhances operational efficiency by 25%, significantly reducing errors. Automated systems streamline the process, minimizing waste and maximizing resource utilization, which is critical in large-scale textile manufacturing.
Real-Time Adjustments for Complex Designs
Real-time adjustments in cutting systems introduce a new level of flexibility, enabling operators to modify cutting parameters dynamically. This is especially beneficial when dealing with intricate label designs, as it allows continuous operation without halts. Consequently, the implementation of these systems can enhance the production of complex label designs by 30%, according to industry statistics. By accommodating design variations seamlessly, real-time adjustments in automated systems foster creative freedom while maintaining production efficiency.
Incorporating these advanced technologies in fabric label production not only enhances accuracy but also significantly reduces waste, thereby offering considerable cost savings. Embracing such innovations is essential for any manufacturer aiming to maintain a competitive edge in the textile industry.
Key Benefits of Automated Label Cutting Solutions
Enhanced Production Speed Without Compromise
Automated cutting solutions significantly boost production speeds by ensuring precise and rapid cuts without sacrificing quality. As manufacturing industries increasingly rely on automation, reports indicate that manufacturers can experience a 40% increase in production efficiency. This improvement results in faster delivery times, enhancing customer satisfaction and allowing companies to meet tight deadlines with ease. By integrating such advanced systems, businesses can maintain high-quality standards while benefitting from increased throughput and reduced operational costs.
Material Versatility Across Textile Types
Advanced automated cutting machines boast the ability to handle a wide range of materials, from delicate lightweight textiles to rugged heavy-duty fabrics, showcasing impressive versatility. This capability extends to multifaceted cutting systems, enabling manufacturers to broaden their product lines and appeal to a more extensive market segment. Case studies highlight how these systems have successfully allowed businesses to cater to diverse customers' needs by adeptly managing different textile types. By offering this level of adaptability and material compatibility, companies can stay competitive in an ever-evolving industry landscape.
Waste Reduction Through Optimal Nesting
Automated systems are designed to optimize the layout and nesting of labels on fabric, leading to a significant reduction in material waste compared to manual methods. This technology ensures that the material is utilized to its fullest potential, minimizing offcuts and contributing to both cost savings and environmental sustainability. According to data, effective nesting techniques can cut material waste by as much as 20%, offering considerable advantages for businesses seeking to improve their resource efficiency. By adopting these waste reduction techniques, manufacturers can achieve not only economic benefits but also align with global sustainability goals.
Advanced Machinery for Precision Label Manufacturing
High-Speed Ultrasonic Cutting Systems
High-speed ultrasonic cutting systems have transformed label manufacturing by ensuring both rapid processing and precise cuts. These machines maintain exceptional operational speeds without compromising on the accuracy essential for quality labels. Investing in such technology significantly enhances throughput, allowing manufacturers to complete large quantities faster while preserving intricate design elements. Such improvements not only shorten processing times but also ensure consistent product quality, meeting the high standards demanded in the industry.
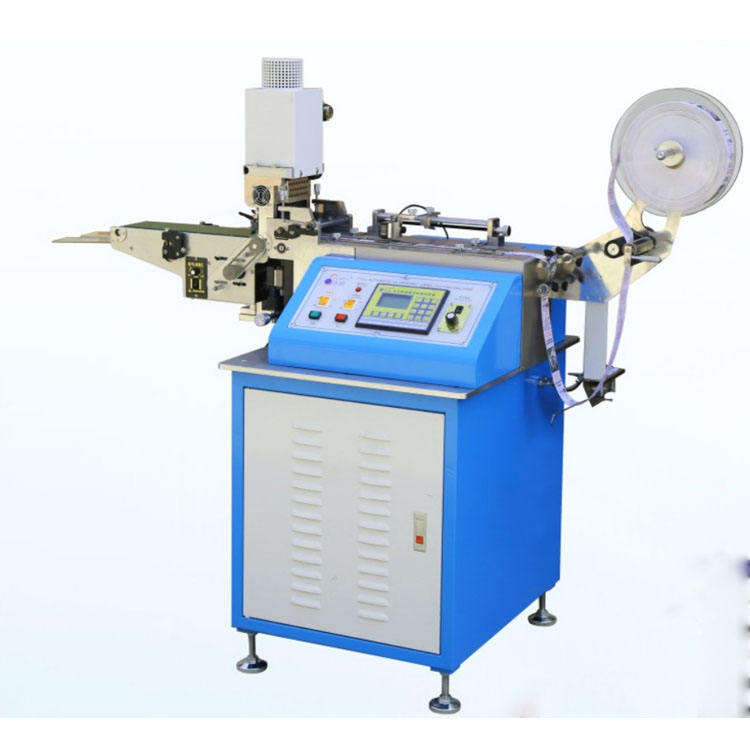
Multi-Functional Screen Printing Integration
Integrating multi-functional screen printing with cutting machinery creates a streamlined workflow, enhancing label production efficiency. This system allows manufacturers to produce cohesive labels through a unified process, eliminating the need for separate printing and cutting stages. By doing so, operational efficiency is bolstered, enabling the quick production of customized labels. Such integration not only saves time but also reduces potential human error, ensuring high-quality outcomes every time.
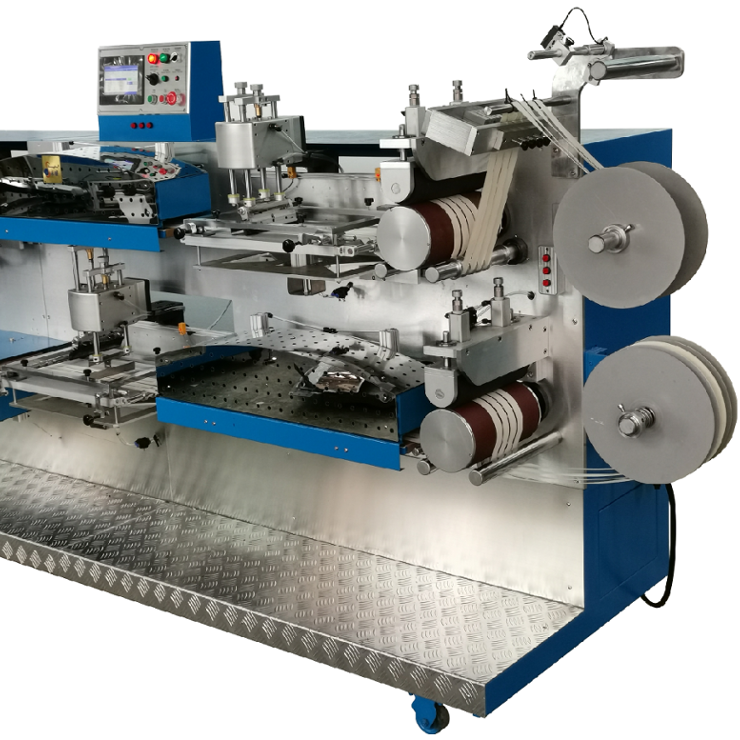
Smart Fabric Handling for Continuous Operation
Smart fabric handling techniques in advanced machinery facilitate continuous operation, accommodating various fabric types seamlessly. These intelligent handling systems minimize downtime by ensuring the smooth transition between different materials, maximizing overall performance. By enabling uninterrupted production, manufacturers experience a tangible boost in productivity. This not only hastens operational workflows but also elevates the potential for handling larger volumes without compromising on quality.
With these advanced machines, businesses can expect to see marked improvements in their production systems, setting a new benchmark for efficiency and precision in label manufacturing.
Implementing Automated Systems: Best Practices
Workflow Integration Strategies
Successfully integrating automated systems into existing workflows demands strategic planning and an understanding of various influencing factors, both technological and human. It is essential to streamline the integration process by analyzing current workflows and identifying potential bottlenecks that automation could address. Simultaneously, it is crucial to incorporate human factors into this transition. Conducting comprehensive training sessions ensures that operational staff can adapt quickly to new systems, minimizing disruption and maximizing the benefit of the automated technologies. This approach aligns with industry best practices for seamless integration and enhanced productivity.
Maintaining Cutting Blade Efficiency
The efficiency and precision of cutting blades are critical for optimal operation of automated systems. Regular maintenance and calibration are necessary to preserve cutting precision and prevent unnecessary downtime, which could otherwise disrupt production schedules. Studies have indicated that blade maintenance protocols can extend the lifecycle of blades by up to 35%. Implementing a routine maintenance schedule not only enhances cutting blade efficiency but also significantly contributes to improving overall operational efficiency, saving costs associated with frequent replacements and repairs.
Quality Control Protocols for Labels
Ensuring high-quality label production necessitates the implementation of stringent quality control protocols. Regular audits on the output help maintain consistency, ensuring all labels adhere to industry standards and customer expectations. Establishing reliable QC protocols not only enhances product quality but also improves customer satisfaction, reducing the rates of product returns and, consequently, boosting profitability. Companies that prioritize strict quality checks for each batch often enjoy a stronger reputation in the market, leading to sustained business growth.
Recommended Products
Hot News
-
Reflect On The Cultural Significance Of The Printing Press In Preserving And Disseminating Knowledge
2023-12-08
-
The Role Of The Printing Press In The Global Economy
2023-12-08
-
Environmental Impact: Analyzing The Environmental Footprint Of The Printing Industry
2023-12-08
-
The Frontier Of Printing: 3d Printing And Its Industrial Renaissance
2023-12-08
-
The Evolution And Impact Of The Printing Press
2023-12-08