How Flexographic Printing Enhances Efficiency in Custom Label Manufacturing
Understanding Flexographic Printing in Label Manufacturing
Core Principles of Flexo Technology
Flexographic printing, often abbreviated as flexo, leverages flexible relief plates to achieve high-speed production. This technology is versatile, allowing prints on a variety of substrates such as plastics, paper, and metallic materials. Flexographic printing is particularly valued for its ability to adapt to different design requirements, providing smooth registration and precise details. The flexible plates used in flexography are designed to deliver high-quality images and text across diverse surfaces, making it a preferred choice for industries that demand customization and efficiency.
In flexo technology, every color in a design requires a separate plate, which enables enhanced image quality. This method accommodates a range of inks, including water-based and UV-curable variants, making it a versatile choice for various printing needs. Its compatibility with additional processes like laminating, embossing, and die-cutting further amplifies its adaptability, allowing businesses to create sophisticated packaging solutions. The rapid advancements in flexographic technology continue to enhance its efficiency and precision in label manufacturing.
Key Components of Modern Flexo Presses
Modern flexo presses comprise several vital components, notably the anilox rollers, flexible printing plates, and advanced drying units. Anilox rollers play a critical role in controlling ink transfer, where they ensure precision while minimizing waste by using engraved cells to hold and release ink onto the plates. This meticulous ink transfer process is essential for sharp and consistent prints.
Another key component is the drying technology, which significantly enhances production efficiency. Flexo presses incorporate innovative drying methods such as hot air, infrared, and UV curing to enable rapid drying while maintaining high-quality prints. This fast-drying capability not only speeds up the production process but also ensures durability and clarity in the final product. The integration of these components in modern flexo presses makes them highly effective for meeting the demands of diverse print jobs, from simple labels to complex multi-color designs.
5 Efficiency Benefits of Flexographic Printing
High-Speed Production Capabilities
Flexographic printing boasts exceptional high-speed production capabilities, making it ideal for industries requiring quick turnaround times. With the capability to achieve speeds of up to 1500 feet per minute, flexographic printing significantly outperforms alternative methods, ensuring that large-scale jobs are completed swiftly. This high-speed production system allows for longer print runs without interruptions, facilitating increased productivity and reduced lead times, crucial for meeting tight deadlines in competitive markets.
Reduced Material Waste Through Precision
Flexographic printing is renowned for its precision, which directly contributes to reducing material waste. The technology's efficient setup means fewer adjustments are needed, minimizing ink waste and ensuring consistent application. This precision not only results in cost savings but also aligns with sustainability initiatives by reducing substrate usage. By delivering precise ink application, flexographic printing aids in producing environmentally friendly labels, appealing to businesses focused on reducing their carbon footprint.
Multi-Process Integration Advantages
Flexographic printing offers significant advantages through its capacity for multi-process integration. This flexibility allows it to seamlessly combine with other printing techniques, such as digital or gravure printing, enhancing production versatility. Such integration enables swift adaptation to dynamic market demands and ensures quicker turnaround times. Businesses benefit from streamlined processes, as they can leverage the strengths of different technologies to deliver varied and high-quality printing solutions.
Quick Changeover Systems
Modern flexographic presses are equipped with quick changeover systems that drastically minimize downtime between jobs. These automated systems streamline the transition from one production to another, supporting a just-in-time manufacturing approach. This capability ensures manufacturers can rapidly align with evolving customer needs, providing efficient production scheduling and maximizing operational efficiency. It's a critical feature for businesses aiming to maintain agility in a fluctuating market landscape.
Consistent Quality Across Long Runs
Consistency in print quality is crucial for maintaining brand integrity, and flexographic printing excels in this aspect across extensive print runs. Advanced monitoring systems within flexo presses maintain registration accuracy and color consistency, preventing errors that could affect the brand image. This assures businesses of high-quality outputs that are crucial in ensuring customer satisfaction and reinforcing brand trust, even during prolonged production cycles.
Flexo vs. Digital: Optimizing Label Production
Cost Comparison for Different Run Sizes
Understanding cost efficiency is crucial when deciding between flexographic and digital printing for label production. Flexographic printing shines in large quantity orders due to its reduced per-unit cost post initial setup. This is because the initial expenses, like manufacturing custom print plates, are distributed over a larger number of units, making it cost-effective for larger runs. Conversely, digital printing, while initially pricier for longer runs, is ideal for smaller batches. It eliminates the need for plates, which significantly reduces setup costs and time. This makes digital printing a more viable option for short runs or when brands need to accommodate quick design changes without incurring additional expenses. The decision between the two methods hinges on the volume of print and the budgetary constraints of the business.
When to Choose Flexo for Maximum ROI
Flexographic printing is particularly beneficial when production volumes exceed 5,000 labels. In such scenarios, the cost efficiencies associated with reduced ink and substrate expenses are maximized, providing a strong return on investment (ROI). Flexo printing offers long-run efficiency, making it suitable for brands that require large scale label production, such as for national product distributions or major retail launches. The method's ability to produce high volumes at lower per-unit costs after the initial setup is significant for businesses aiming for widespread brand visibility. Additionally, the advanced color matching techniques employed in flexographic printing ensure consistent quality, which is vital for maintaining brand integrity across numerous labels. For companies focused on large-scale productions, flexographic printing offers a powerful combination of cost efficiency and high-quality outputs.
Advanced Flexo Solutions for Custom Labels
High-Quality DR EAS Label All-In-One Machine
The High-Quality DR EAS Label All-In-One Machine revolutionizes the label production landscape by integrating multiple functionalities into a single system, optimizing the production of both security and promotional labels. This innovative machine not only facilitates seamless label application but also incorporates cutting-edge features like brand verification and theft prevention, thereby enhancing the market competitiveness of retail businesses. Designed with precision, it supports various label sizes and types, making it versatile for different product requirements. Its advanced capabilities ensure that businesses can achieve error-free applications efficiently.
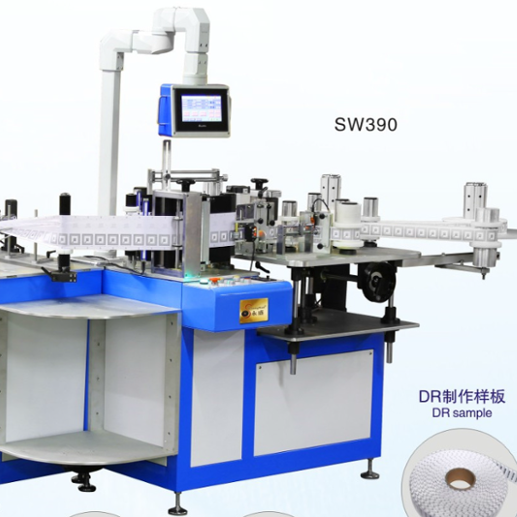
RFID Labeling Machine Integration
The integration of RFID capabilities in labeling machines like the RFID Labeling Machine significantly streamlines inventory management while enhancing tracking accuracy. This advanced system allows for seamless placement of RFID chips during the labeling process, ensuring that each product is tagged accurately and efficiently. When combined with flexo printing systems, it offers high-quality printing results, supporting a range of materials and tag types. This integration provides companies with a strategic advantage by improving supply chain transparency and operational efficiency.
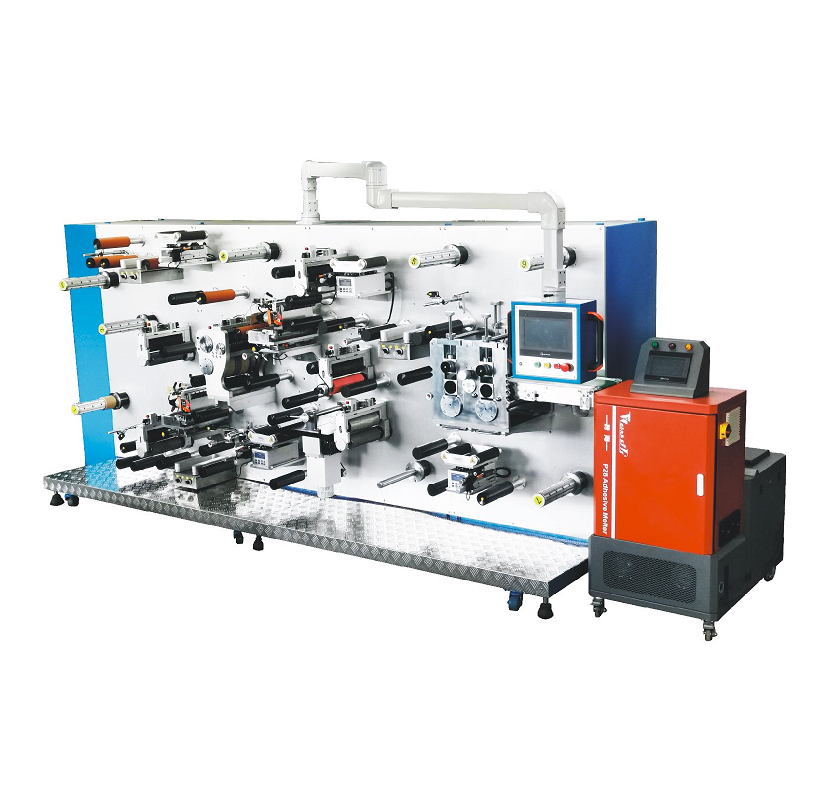
2024 High-Speed Three Colors Flexo Clothing Printer
The 2024 High-Speed Three Colors Flexo Clothing Label Printing Machine elevates clothing label production through its high-speed capabilities and versatility in color options. With its advanced flexographic printing technology, this machine supports customizations and short printing runs without compromising on print quality. It meets the diverse demands of the clothing and textile industry, providing businesses with a robust solution for high-quality, multi-color label printing while maintaining efficiency and reducing production time.
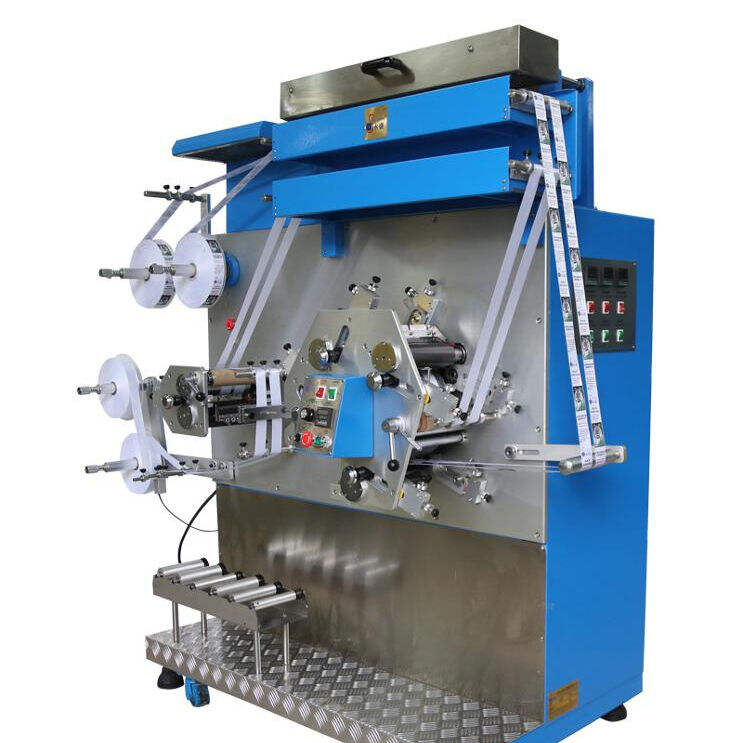
Future Trends in Flexo Label Manufacturing
Eco-Friendly Ink Innovations
The move towards eco-friendly ink innovations is a significant trend shaping the future of flexo label manufacturing. As the industry increasingly embraces sustainability, there is a growing shift towards bio-based and water-soluble inks which help reduce environmental impact. A major advantage of these eco-friendly inks is their potential to enhance a brand's image, resonating well with consumers who prioritize sustainability. In the printing sector, this shift not only aligns with global ecological goals but also potentially boosts brand loyalty and sales.
AI-Driven Process Optimization
AI-driven process optimization is revolutionizing flexo label manufacturing by enhancing operational efficiency and product quality. The integration of artificial intelligence allows for predictive maintenance of printing equipment, significantly reducing downtime and prolonging the lifespan of machines through timely intervention. By employing data analytics, manufacturers can fine-tune print processes to achieve superior consistency and precision, ultimately enhancing the quality of the finished product. Furthermore, AI technologies empower manufacturers to maximize resource utilization, streamline workflows, and adapt swiftly to market demands, positioning them as frontrunners in the competitive printing landscape.
Recommended Products
Hot News
-
Reflect On The Cultural Significance Of The Printing Press In Preserving And Disseminating Knowledge
2023-12-08
-
The Role Of The Printing Press In The Global Economy
2023-12-08
-
Environmental Impact: Analyzing The Environmental Footprint Of The Printing Industry
2023-12-08
-
The Frontier Of Printing: 3d Printing And Its Industrial Renaissance
2023-12-08
-
The Evolution And Impact Of The Printing Press
2023-12-08